Advantages of Riveting vs. Bolting or Welding
.png)
What are the advantages of riveting vs. bolting or welding?
More importantly, Why does it matter?
Mainly, knowing the differences and advantages of riveting enables you to make the best choices for your specific needs.
Specifically, these include:
- Optimal Joint Selection: Knowing the benefits of riveting enables you to choose the method that best aligns with your requirements for strength, durability, material compatibility, vibration resistance and cost effectiveness.
- Quality and Durability: Better resistance to vibration and stronger joins ensures the longevity and reliability of riveting.
- Material Versatility: Flexibility in design and material selection opens up new possibilities for creative and innovative product development.
- Cost Efficiency: By choosing cost-effective joining methods like riveting, you can improve the bottom line and stay competitive in the market.
- Operational Efficiency: Simplified assembly procedures, lower labor costs and requirements, and shorter assembly times can streamline production workflows and boost overall efficiency.
- Product Performance: Riveting superior strength, durability and vibration resistance versus other joining methods results in end users who are more likely to trust and value products that show this level of quality and longevity.
In a nutshell, understanding the advantages of riveting over other joining methods enables you to make informed decisions for better cost efficiency, operational effectiveness, and improved product quality.
Now let’s look at the advantages of riveting...
1. Heat-Free Process
Riveting is a heat-free joining method that avoids problems associated with heat-based methods. For example, thermal expansion and metal damage caused by welding can be a problem. By fastening metals without heat, riveting avoids these potential issues.
2. Provides Strength Inside and Out
There are also strength differences. Riveting creates joints from the inside out. This results in stronger and more durable connections than welding, which only joins the exterior surfaces of the parts.
3. More Material Options
Riveting also provides a greater number of material options. It allows for the joining of different materials, including non-ferrous metals. Non-ferrous metals (e.g., copper, aluminum, lead, zinc, and nickel) do not contain significant amounts of iron, which makes them more resistant to corrosion than ferrous metals.
This versatility is unmatched in applications that require diverse material combinations. For instance, building facades may combine glass, steel and aluminum to create visually appealing and weather-resistance structures.
Resistance to Vibration
In industries where vibrations from constant movement can create problems with welded or bolted joints, such as in the automotive industry, riveting provides superior vibration resistance.
Cost Effective
From a cost perspective, riveting is usually more cost effective than welding and bolting because of the less need for specialized equipment and skilled labor. Riveting requires simpler tools and equipment. This means lower upfront investment costs. Plus, the simpler process of inserting and deforming rivets lowers assembly time and labor costs.
For more information on this topic, check out THIS post on blind rivets or another perspective of bolts and nuts over welds HERE.
About the Author
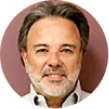
Started my career in the fastener world in 1969 at, Parker Kalon Corp. a NJ based screw manufacturer located in Clifton, NJ working in inventory control, scheduling secondary production and concluding there in purchasing. In 1971 I accepted a sales position at Star Stainless Screw Co., Totowa, NJ working in inside sales and later as an outside salesman, having a successful career at Star I had the desire with a friend to start our own fastener distribution company in 1980 named: Divspec, Kenilworth, NJ. This was a successful adventure but ended in 1985 with me starting Melfast in August 1985 and have stayed competitive and successful to date. Melfast serves the OEM market with approximately 400 accounts nationally.