Why Fastener Coatings Matter
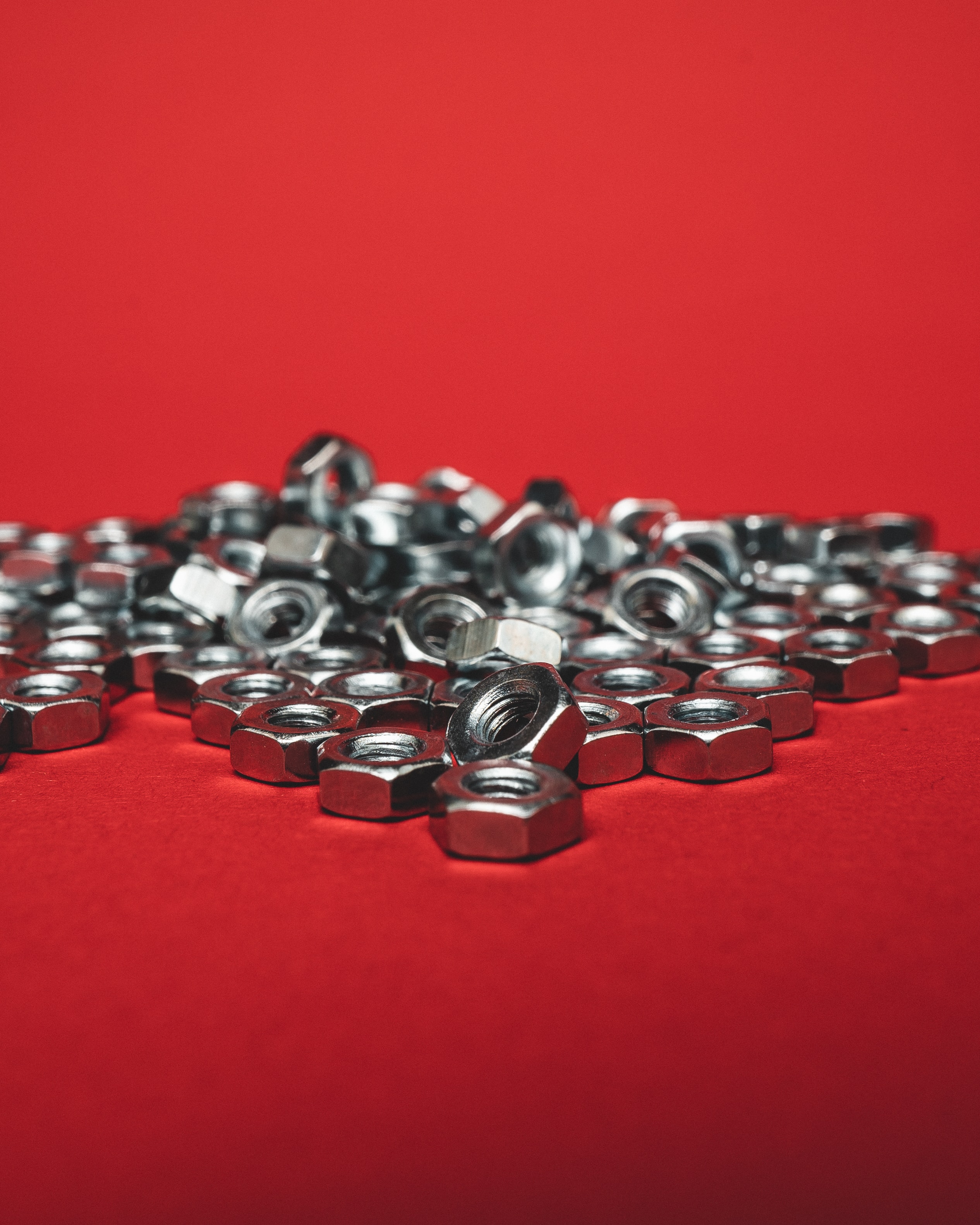
Why Fastener Coatings Matter
Selecting the right coating for your fasteners is not a decision to be taken lightly. The coating affects several key factors that not only affect the functionality of the fastener, but also the integrity of your entire project.
Here’s how:
Corrosion Resistance: How well the fastener will stand up against environmental factors like water, salt, and chemicals.
Aesthetics: The look of your fasteners can be essential, especially in high-visibility and decorative applications.
Friction Levels: Different coatings have varying frictional properties. The right coating can reduce friction during installation, making your assembly process more efficient.
Wear Resistance: A coating that resists wear will ultimately extend the lifespan of both the fastener and the material it's fastening.
Electrical Conductivity or Insulation: In specialized applications, the electrical properties of a coating might be a crucial factor.
A Guide to Popular Coating Types
Before we dig into the specifics, here's a quick rundown of some commonly used fastener coatings:
Zinc Coatings: Good for corrosion protection, especially in indoor settings.
Zinc-Nickel Coatings: Offers enhanced protection, particularly at high temperatures.
Phosphate Coatings: Primarily used as a base for paint or to reduce friction during installation.
Cadmium Coatings: Very corrosion-resistant but carry environmental and health concerns.
Polymer Coatings (e.g., Xylan, PTFE, Teflon): Excellent for reducing friction.
Hot-Dip Galvanizing: Ideal for outdoor applications due to its thick, durable zinc coating.
Spotlight on Specific Coatings
Zinc Plated
Zinc-plated fasteners are your go-to for indoor applications. These cost-effective fasteners are corrosion-resistant to a degree. Plus, their shiny finish makes them eye-appealing when aesthetics are important.
Zinc Yellow Plated
If you're in the automotive sector, consider zinc yellow plated fasteners. They offer enhanced corrosion resistance and are easily identifiable thanks to their distinct yellow hue.
Black Oxide Plated
Ideal for settings like photography studios or theaters where reduced light reflection is critical. These fasteners also offer mild lubrication, aiding in smoother installation.
Black Zinc Plated
If you're after the aesthetic benefits of black oxide but need better corrosion resistance, black zinc is your solution.
Mechanical Galvanized
When corrosion and abrasion resistance are a major concern, mechanically galvanized fasteners are the way to go. Plus, they're more environmentally friendly.
Nickel Plating
Nickel plating offers a versatile choice with moderate to high corrosion resistance. Nickel-plated fasteners are durable, wear-resistant, and possess a shiny finish, which is often desirable. They're chemically stable, conduct electricity well, and can even be soldered with ease. But keep in mind, nickel is more expensive and can be brittle under extreme conditions.
Selecting the right fastener coating is much more than a cosmetic choice—it's a long-term investment in the quality of your project.
We offer a range of fasteners with different coatings to suit various applications. So the next time you're caught between zinc and nickel, or black oxide and mechanical galvanized, use this guide as your go-to resource.
Or call (973-227-0045) or email ([email protected]) for expert advice on your specific project needs.
Photo by Mika Baumeister on Unsplash
About the Author
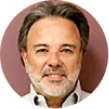
Started my career in the fastener world in 1969 at, Parker Kalon Corp. a NJ based screw manufacturer located in Clifton, NJ working in inventory control, scheduling secondary production and concluding there in purchasing. In 1971 I accepted a sales position at Star Stainless Screw Co., Totowa, NJ working in inside sales and later as an outside salesman, having a successful career at Star I had the desire with a friend to start our own fastener distribution company in 1980 named: Divspec, Kenilworth, NJ. This was a successful adventure but ended in 1985 with me starting Melfast in August 1985 and have stayed competitive and successful to date. Melfast serves the OEM market with approximately 400 accounts nationally.