Advantages of Modern Deck Screws in Building Durable Decks
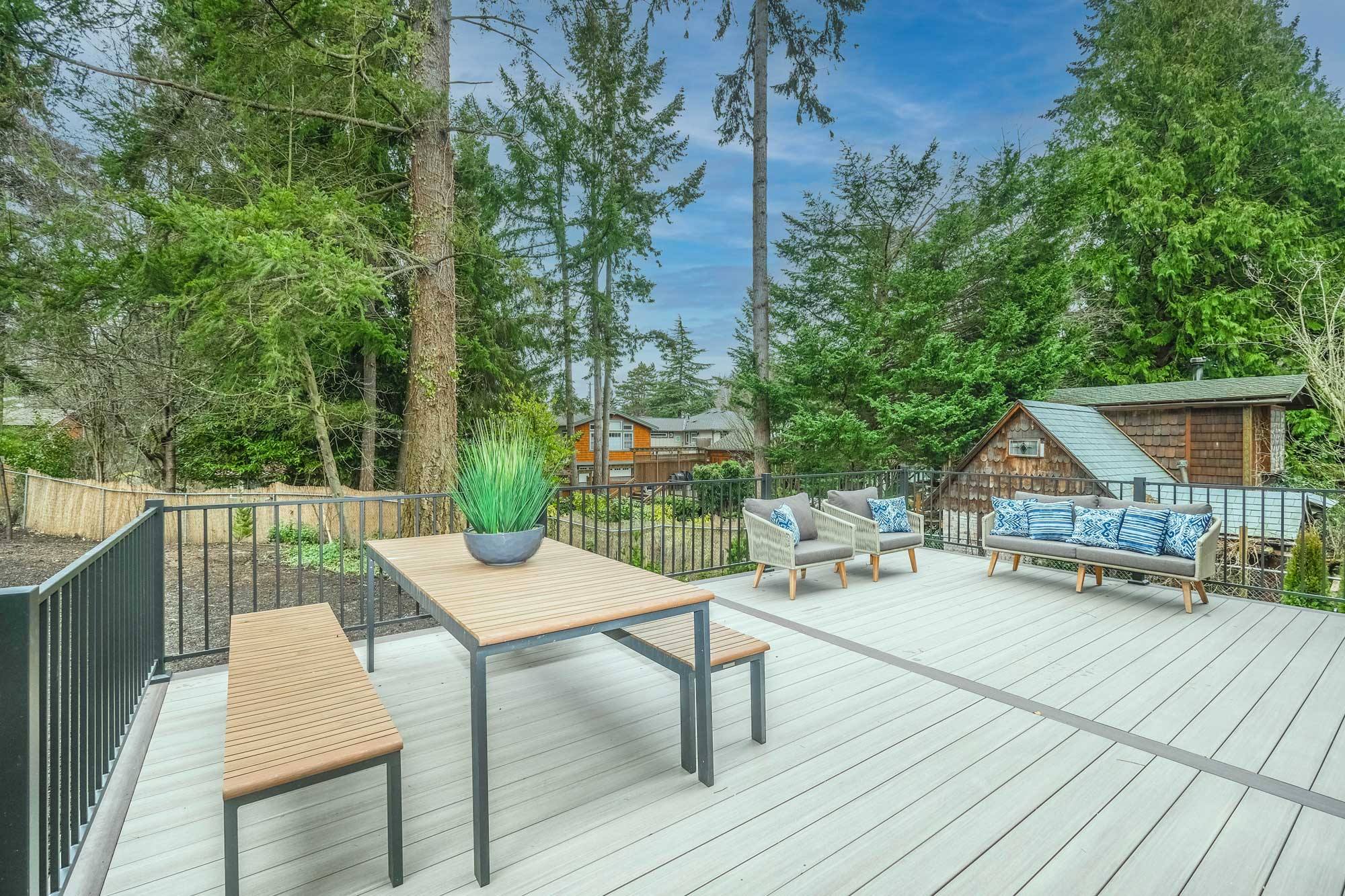
Deck screws may be the unsung heroes of the fastener world. They can withstand just about any type of environmental challenge you throw at them.
Extreme hot or cold?
No problem.
Chemical exposure?
No sweat.
Wind loads?
Holding fast.
It’s no wonder deck screws make the perfect fastener when you’re in need of a reliable outdoor deck structure.
Better yet, new modern innovations in the industry provide more options than ever, helping you find the best deck screw version for your project – aesthetically and structurally.
First, here’s a quick review of exactly what makes deck screws so valuable, particularly to the building and construction industries…
Deck screws directly fasten the deck boards to the joists, creating a solid connection. They prevent deck boards from shifting and loosening over time.
Most of them are designed with combinations of material that provide superior strength and resistance to damage. Screws made out of stainless steel and carbon are a great example. Low quality screws, on the other hand, are likely to have more complications during and after use, including snapping during installation.
Overall, advantages of deck screws include:
- Reduced Splitting and Cracking
Deck screws' controlled insertion minimizes the risk of splitting or cracking deck boards. And deck screws specifically designed for outdoor applications prevent damage to the wood and add to the longevity of the structure. A win-win all around. - Versatility
Deck screws are not limited to deck construction but can also be used for various woodworking projects. They’re suitable for both interior and exterior applications. This makes them practical and reliable in a wide range of manufacturing processes. - Weather Resistance
As previously mentioned, deck screws are made from corrosion-resistant materials, such as stainless steel, to ensure durability against weather elements.
Using a less robust fastener for an outdoor decks exposed to moisture and temperature fluctuations is a recipe for structural disaster. Especially in the long term.
Deck screws also possess several unique features…
Self-drilling or self-tapping. Self-drilling or self-tapping features indicate that they have a sharp point and special threads that enable them to drill their own pilot holes and tap into the material without pre-drilling.
Coarse threads and a range of head types. Deck screws also typically have coarse threads specifically designed to provide a stronger grip and better holding power in wood and other materials.They’re available in various head types, including flat, bugle, and trim heads.
The choice of head type and color depends on the specific application and the desired aesthetic or functional requirements you want to achieve. (Call us if you’re unsure which is most suitable for your project.)
Endless array of colors. The first deck screws were available in only five colors. Today you’ll find a limitless choice of deck screw colors to suit your project. This results in a more seamless and visually appealing finish.
Last and far from least, deck screws are designed to withstand substantial loads and stresses. They’re engineered to provide strong connections between materials, making them ideal for applications where structural integrity is critical.
Buying high-quality deck screws provides longevity and overall greater value for your money.
About the Author
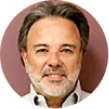
Started my career in the fastener world in 1969 at, Parker Kalon Corp. a NJ based screw manufacturer located in Clifton, NJ working in inventory control, scheduling secondary production and concluding there in purchasing. In 1971 I accepted a sales position at Star Stainless Screw Co., Totowa, NJ working in inside sales and later as an outside salesman, having a successful career at Star I had the desire with a friend to start our own fastener distribution company in 1980 named: Divspec, Kenilworth, NJ. This was a successful adventure but ended in 1985 with me starting Melfast in August 1985 and have stayed competitive and successful to date. Melfast serves the OEM market with approximately 400 accounts nationally.