Effective Measures To Minimize Fastener's Thread Galling
Even though thread galling is a frequent occurrence during the tightening processes, the truth is that the problem is not always understood. Often referred to as cold-welding process, galling develops on the surface of the threads that are placed under heavy pressure. Perhaps the most frustrating aspect is that although threaded bolts pass all initial inspections and testing, they still fail to perform their task.
Some fasteners are innately more sensitive to galling
As any fastener manufacturer can confirm, stainless steel threaded bolts are usually more susceptible to galling compared to their galvanized counterparts. On a side note, galling is a process that typically occurs in alloys that are capable of generating an oxide surface film on their own. When exposed to heavy pressures, the thin film of protective oxide is destroyed as the force accumulates between the threads. With the coating gone, the metal threads remain bare and are exposed to one another, which leads to friction. These factors are able to generate sufficient heat to fuse the bolt and nut together.
The risks of galling
In spite of the fact that minor galling causes only slight damage at the surface of the threads, the fastener needs to be replaced as soon as possible. Removing the fastener in severe cases of galling is usually problematic because at that point, the nut and bolt are welded together pretty tightly. In the event that the galling process occurs during the tightening and the fastening continues, then there’s a fair chance the threads will be stripped.
Measures to minimize galling
As previously mentioned, engineers have a difficult time understanding the mechanism behind galling. Even though galling cannot be successfully eliminated, there are several things engineers can do to minimize the process:
- Thread lubrication
Because friction appears to be the key factor that leads to galling, a possible solution would imply thread lubrication. However, if you choose to employ this method, then be aware that you need to adjust the torque-tension relationship after adding the lubricant. Alternatively, you could consider applying a PTFE based coating to the stainless steel fasteners.
- Reducing the wrench speed during installation
Along with friction, heat is an equally important factor that can lead to galling. Then again, don’t forget that these processes are intertwined, meaning that generating friction automatically results in heat. The phenomenon can be observed in applications that require an increase in speed during installation. In the light of these facts, it’s understandable why a reduction of the wrench speed during installation and removal could minimize galling.
- Avoiding torque lockdowns
Since torque lockdowns add further resistance to the threads – and hence, more friction and heat – you should avoid them at costs.
- Coarse threading
Because coarse threads are less prone to galling compared to fine threads, you can use 2A-2B fit coarse threads if the application allows it. In case you didn’t know, the coarse threads are larger and can take some abuse during handling.
See the below video for more details on how to avoid galling
About the Author
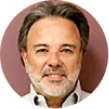
Started my career in the fastener world in 1969 at, Parker Kalon Corp. a NJ based screw manufacturer located in Clifton, NJ working in inventory control, scheduling secondary production and concluding there in purchasing. In 1971 I accepted a sales position at Star Stainless Screw Co., Totowa, NJ working in inside sales and later as an outside salesman, having a successful career at Star I had the desire with a friend to start our own fastener distribution company in 1980 named: Divspec, Kenilworth, NJ. This was a successful adventure but ended in 1985 with me starting Melfast in August 1985 and have stayed competitive and successful to date. Melfast serves the OEM market with approximately 400 accounts nationally.