Top 5 Reasons Why You Should Stay Away From Nylon Fasteners
You can blame it on their very attractive price, but nylon fasteners seem to be all the rage these days. Without denying the fact that they work just fine for a variety of applications, especially in the electronics and medical fields, it is necessary to mention that the material has several weaknesses.
Simply put, unlike metal fasteners, their nylon counterparts are more likely to fail under extreme pressure. Let’s explore the situations when you would be better off with the standard metal fasteners.
- Nylon should never be used in marine applications
Granted, certain plastics like Isoplast, PET or PVC are not only hydrophobic, but they are also unaffected by saltwater, gasoline or other known corrosive substances. On the other hand, nylon is a hygroscopic material meaning that it attracts and absorbs the water in the surrounding environment. The reason for this stems from its unique composition that features water molecules suspended between the molecules of the material. When used in boating or marine applications, nylon will swell and degrade relatively quickly.
- Nylon doesn’t share the UV and chemical resistances of other plastics
If you leave nylon out in the sun, you will notice that it start to degrade, turning yellow and becoming brittle relatively quickly. Moreover, it performs very poorly in acid environments specific to various industrial applications. While it does show some resistance when exposed to ketones and hydrogenates hydrocarbons, it is still affected by these substances. Therefore, nylon is contraindicated for industries that imply working with acids and halogens.
- Nylon can’t withstand high temperatures
Considering that the nylon’s continuous service temperature does not exceed 121 degrees Fahrenheit, fasteners made of this material should never be employed in the construction of ovens or machines that heat up during utilization. If you really have to use plastic fasteners, then Teflon is a much better choice. As a side note, metal fasteners are always the best choice for industries that involve operating machinery that can reach high temperatures.
- Nylon is highly flammable
In addition to not being able to maintain its properties under high temperatures, nylon is also flammable. Flammable in this case doesn’t mean that a nylon fastener will immediately catch fire when it comes into contact with an open flame, but rather that it will melt. Needless to state that once the fastener melts, the machine it was holding together becomes a hazard and you risk setting the entire facility ablaze.
- Nylon is not strong enough for engineering applications
Thanks to the recent innovations in the field, plastic fasteners that are strong enough to replace metal became a real hype. However, nylon is not among the plastics that fall under this category and the 10,000 PSI threshold is proof of that. Not only are nylon fastener not reliable in industries that require higher strength, but the material doesn’t even come close to a replacement for metal fasteners. Consequentially, if you’re searching for competent fasteners for mining, highway constructions, railroad or modular building, it would be wise to choose fasteners made of copper or cast iron.
About the Author
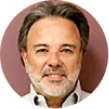
Started my career in the fastener world in 1969 at, Parker Kalon Corp. a NJ based screw manufacturer located in Clifton, NJ working in inventory control, scheduling secondary production and concluding there in purchasing. In 1971 I accepted a sales position at Star Stainless Screw Co., Totowa, NJ working in inside sales and later as an outside salesman, having a successful career at Star I had the desire with a friend to start our own fastener distribution company in 1980 named: Divspec, Kenilworth, NJ. This was a successful adventure but ended in 1985 with me starting Melfast in August 1985 and have stayed competitive and successful to date. Melfast serves the OEM market with approximately 400 accounts nationally.